What Information Should You Put on Wire Markings?
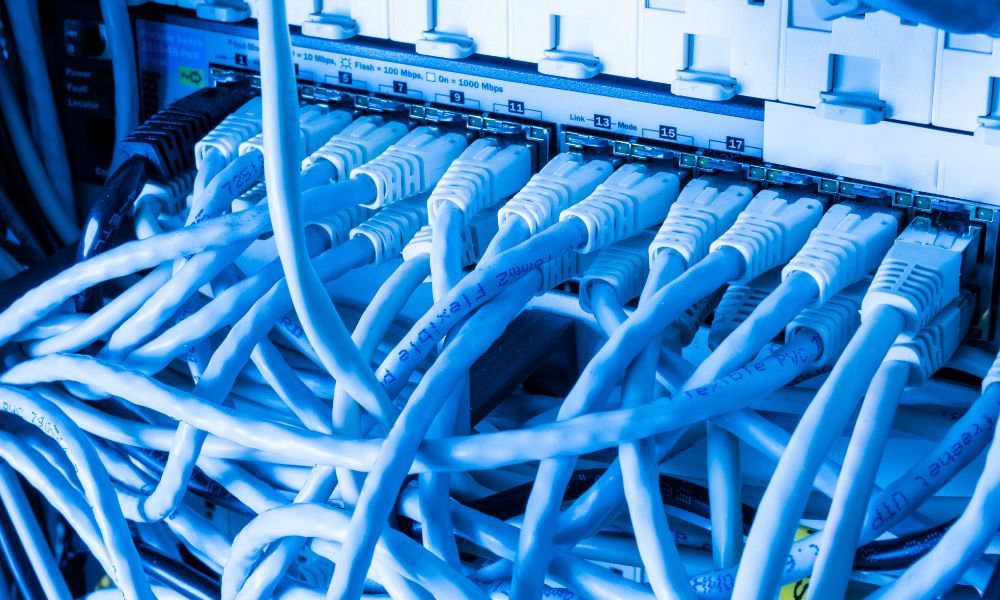
Wire labels for electrical cables and conductors are integral for safety and utility. With hundreds or thousands of cables going in different directions, it’s practically impossible to conduct maintenance or repair an electrical system. Learn what information you should put on wire markings for safety and efficiency.
Marking Requirements for Conductors & Cables
The labels a wire needs depend largely on their setting and application. The National Electrical Code (NEC) establishes marking requirements, which include basic marking rules for conductors and cables.
The NEC states that installers and inspectors must confirm that wires have the following markings:
- Voltage
- Manufacturer’s name/trademark
- American Wire Gauge (AWG) size
- Install date
Other information that should be on wire markings includes where the neutral conductor is smaller than the grounded conductors, but that can vary per industry. Consult industry codes and guidelines to confirm your cords have the necessary information.
Why Laser Marking Is Best for Wires
While you can marking wires in many ways, laser marking has many advantages over inkjet or hot stamping. We’ll explain why laser marking is best for cables.
Versatility
A major benefit of laser wire marking is its versatility for different materials. The laser doesn’t damage the wire material at all—it uses concentrated energy to heat the material beneath its surface and discolor it without affecting the structural integrity.
Hot stamping and inkjet marking make imprints and indents on wires that are not compatible with thin wire insulation common in aviation and manufacturing.
Speed
Another significant advantage of laser marking for manufacturers is that it’s fast. Hot stamping and inkjet printing require many moving parts and consumables to create a permanent label marking.
Since other methods carry a greater risk of damaging the wire material, more quality control inspections are necessary to ensure the cable and label are satisfactory. Laser wire marking is much faster and more efficient, and it requires less quality control inspection because it poses fewer risks to the cable.
Reliability & Precision
As we discussed, inkjet and hot stamping wire labeling methods can go wrong because they have so many moving parts. Laser wire marking is more reliable because it’s much simpler with immediate results. Since most of the laser wire marking process is automated, there’s less room for operators to make mistakes. Laser marking is also the most accurate, as lasers can be precise within 0.0001 inches!
Conclusion
If you think you or your organization could benefit from utilizing laser marking for cables, you can find a high-quality laser wire marking machine from Tri-Star Technologies. Browse our inventory or contact our expert staff today.