Choosing a Laser Marking System for Heat-Sensitive Materials
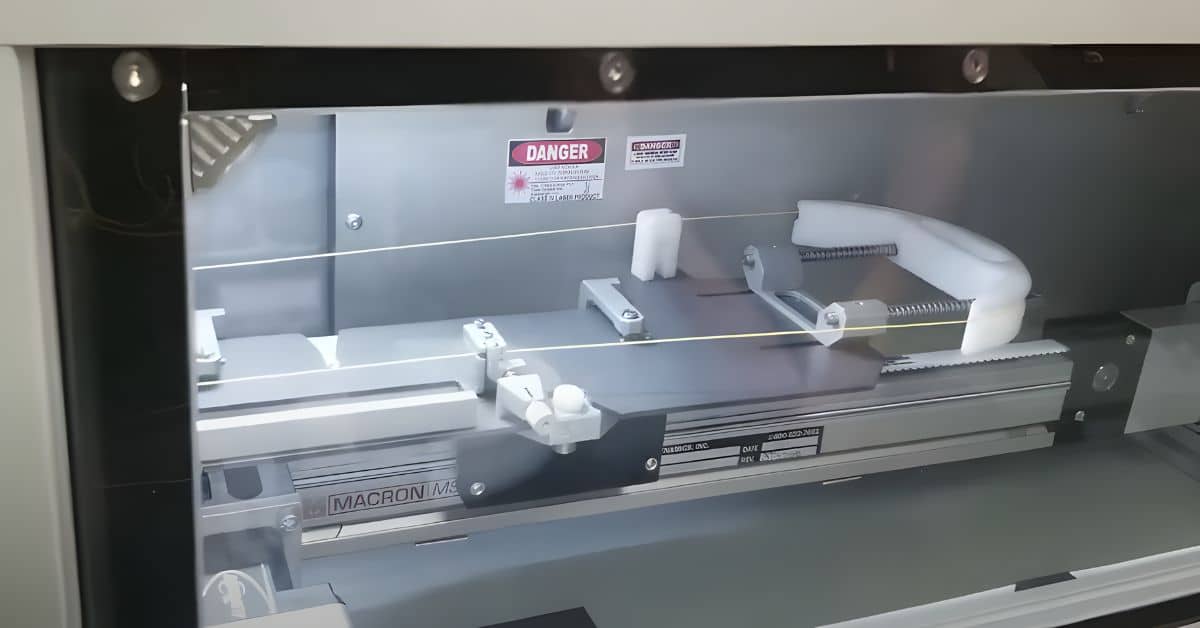
Industries like aerospace and advanced manufacturing heavily rely on laser marking systems to meet stringent requirements for labeling and traceability. However, working with heat-sensitive materials introduces an additional layer of complexity. Traditional marking methods can damage these materials, compromising their integrity and performance.
This is where advanced laser technologies, particularly UV laser marking systems, offer a reliable and nondestructive solution. In this blog, we’ll explore the many considerations operators and managers must weigh when choosing a laser marking system for heat-sensitive materials. We’ll also provide insights into industry challenges and innovative solutions from leaders like Tri-Star Technologies.
Understanding Heat-Sensitive Materials in Laser Marking
Heat-sensitive materials refer to substrates that are highly susceptible to damage under exposure to high temperatures. Common examples in the aerospace and manufacturing industries include lightweight polymers, specialized coatings, and composite materials. These materials offer exceptional performance properties, such as lightweight construction, but they pose significant challenges under traditional marking methods.
Traditional marking techniques, such as hot stamping or inkjet printing, often generate excessive heat or involve physical pressure. This can melt, warp, or degrade the material, compromising durability and functionality. For instance, hot-stamped marks on thin wire insulations can result in structural damage, prompting leading manufacturers like Boeing to mandate alternative techniques. This drives the industry toward advanced solutions like UV laser marking systems, which are ideal for delicate substrates.
A Comparison of Marking Technologies
To choose a laser marking system for heat-sensitive materials, you must first understand the various marking technologies available. Hot stamping, inkjet marking, and UV laser marking are all examples of marking methods manufacturers may utilize.
Hot Stamping
Hot stamping involves pressing a heated typeface against the material to transfer ink or foil markings. While this method is cost-effective for general use, its high temperatures and pressure make it unsuitable for thin or heat-sensitive materials. Regulatory standards in industries like aerospace further limit its use to nonessential applications.
Dot Matrix Marking
Dot matrix systems create marks by forming individual dots with repeated laser pulses. While this method reduces heat contact compared to hot stamping, it struggles with intricate details and produces marks with limited durability on heat-sensitive surfaces.
Inkjet Marking
Inkjet technology uses liquid ink to create printed markings on material surfaces. Popular in fast-paced industries, these systems offer high-speed, programmable capabilities.
However, the marks are prone to wear, and the curing process for conventional ink still involves some heat exposure. This makes it suboptimal for demanding applications requiring long-term traceability.
UV Laser Marking
UV laser marking is the gold standard for heat-sensitive materials. Unlike other methods, it employs a high-frequency ultraviolet laser beam to create marks by inducing a chemical reaction within the material’s pigment.
This process generates minimal heat, ensuring surface integrity and material durability. With unparalleled precision and nondestructive properties, laser marking machines are the preferred choice for aerospace and advanced manufacturers.
Why UV Laser Marking Is Ideal for Heat-Sensitive Materials
The principles of UV laser marking set it apart from other technologies. By using a 355 nm solid-state ultraviolet laser, these systems focus intense energy into a small area, enabling high precision during the marking process.
Instead of burning or melting the surface, UV lasers trigger a process called photochemical ablation or pigment color change. This makes UV marking highly effective on materials containing titanium dioxide (TiO2), a common pigment used in aerospace-grade polymers.
Advantages of UV Laser Marking
UV laser marking offers many benefits. Its nondestructive application process and compliance with rigorous standards make it widely popular in industries like aerospace and automotive manufacturing.
Nondestructive Application
UV laser marking technology preserves the structural integrity of sensitive substrates by minimizing heat input, ensuring material reliability even in high-performance applications.
High Precision and Resolution
UV laser marking supports intricate designs, alphanumeric characters, barcodes, and logos while maintaining exceptional clarity and contrast.
Durability and Longevity
This special marking technology creates marks that are indelible and wear resistant. Furthermore, they retain contrast over extended periods and withstand harsh conditions, including high temperatures and prolonged UV exposure.
Compliance With Rigorous Standards
UV laser marking meets rigorous specifications such as SAE AIR5558 and BAC5152, ensuring durability, legibility, and traceability in line with the demands of leading manufacturers.
Key Considerations for Choosing a Laser Marking System
While laser marking is ideal for heat-sensitive materials, not every marking system is the same. Selecting the right laser marking system for heat-sensitive materials involves evaluating several factors to ensure compatibility with your manufacturing needs and industry standards.
Material Compatibility
Your chosen laser system must work seamlessly with the materials you use. For industries relying on heat-sensitive polymers, a UV laser system that leverages titanium dioxide-induced color changes is critical. This ensures permanent marks without compromising material properties.
Precision and Resolution
When dealing with aerospace-grade wires or medical tubing, precision and resolution are nonnegotiable. High-resolution capabilities allow clear, intricate markings, making it easier to trace parts and comply with regulatory requirements.
Compliance With Industry Standards
For sectors like aerospace and defense, compliance with strict specifications such as MIL-W-5088L and BAC5152 can make or break a project. Ensure the laser system you select meets these standards to maintain operational integrity and product quality.
Flexibility and Customization
Different projects may call for unique requirements, such as variable font sizes, multiple line markings, or specialized graphics. Laser systems that offer flexible programmable settings enable faster adaptation to new tasks, improving operational efficiency across diverse applications.
Solutions From Tri-Star Technologies
Tri-Star Technologies stands out as a global leader in advanced laser marking solutions for heat-sensitive materials. Their innovations exemplify cutting-edge technologies that prioritize durability, precision, and compliance.
M100L-FG-TT-A Tabletop UV Laser Marker
The M100L-FG-TT-A is a fully automatic UV laser system featuring a 355 nm solid-state laser. With its ability to handle wires ranging from 26 AWG to 4 AWG, it meets all military and commercial specifications. This system supports unlimited text customization, graphics, logos, barcodes, and more, ensuring exceptional versatility for aerospace and manufacturing professionals.
Econolase Portable Wire Marker
Ideal for low-volume runs, the Econolase system offers portability without sacrificing performance. Weighing under 35 pounds, this device is perfect for marking tasks that require flexibility and precision on the go.
M100L-FG-CT UV Laser Wire & Cable Marker
The M100L-GF-CT UV Laser Wire and Cable Marker is an automated system for high-speed operations that delivers unmatched efficiency. This machine can handle production rates of up to 100 feet per minute. With a Class 1 safety rating, it is ideal for industrial facilities requiring full compliance with aerospace standards.
Future-Proof Your Marking Processes With Tri-Star Technologies
Selecting the right laser marking system for heat-sensitive materials is a significant decision for aerospace engineers and manufacturing professionals. UV laser marking offers the most viable solution for preserving material integrity while ensuring compliance and durability. With proven performance across industries, Tri-Star Technologies continues to lead the way in innovative marking systems.
To explore the full range of cutting-edge laser systems, visit Tri-Star Technologies, or contact our team of experts. Enhance your operations, and ensure precision with solutions tailored to the demands of modern manufacturing.