How To Ensure Quality With Industrial Marking Systems
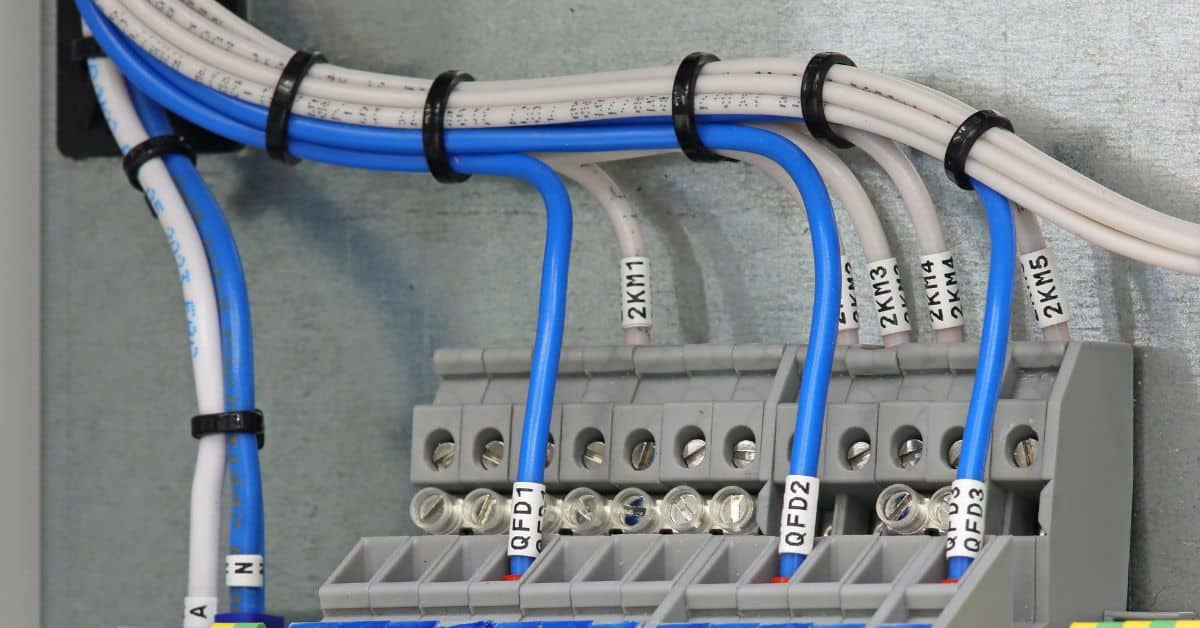
When it comes to industrial wire marking, quality is always the priority. Industrial marking systems are integral to legibility and adherence to regulatory standards In industries where quality and compliance are crucial, like aerospace manufacturing.
For engineers and manufacturers, ensuring quality with industrial marking systems isn’t a choice but a requirement. Below, we dive deep into quality assurance for wire marking systems with a specific focus on its importance within aerospace wire marking.
Challenges in Industrial Wire Marking
Before we get into the industrial marking systems and methods, we must review the challenges that manufacturers encounter in industrial wire markings. Industrial wire marking faces many complications, especially in the areas of bonding, molding, and potting wire assemblies.
These processes can negatively affect the readability of wire markings, often leading to low wettability that hinders the adhesion of marking inks. To tackle these issues, manufacturers must utilize sensitive wire marking methods and other solutions, such as plasma treatment, to enhance surface properties and improve marking adhesion.
Direct Printing Methods for Wire Marking
To meet the unique demands of sensitive wire marking, manufacturers have developed several methods to mark wires accurately and efficiently. Among these, hot stamping, dot matrix, inkjet, and UV laser marking stand out. Hot stamping, one of the oldest methods, involves pressing a heated typeface onto the wire insulation. While effective, it requires constant monitoring to prevent wire damage and is generally reserved for non-essential wires due to its limitations with thinner insulations.
Dot matrix and inkjet marking systems are alternatives, providing non-contact printing capabilities. These methods offer programmability and speed, making them popular in the industry. However, there are still issues regarding mark durability that users must address with other solutions, like plasma surface activation.
Advantages of UV Laser Marking
Among all methods, UV laser marking stands out as the most advanced technique for industrial wire marking, offering quality, durable marks that comply with industry standards. Unlike hot stamping, which can damage materials and produce inconsistent results, UV laser marking is non-destructive and ensures the integrity of the wire insulation.
Non-destructive UV laser marking also outperforms dot matrix methods, which result in lower resolution and less precise markings, and inkjet printing, which may fade or smudge over time. The precision of UV lasers creates sharp, clear markings that are resistant to abrasion and environmental factors. This reliability makes UV laser marking the superior choice for industries that require consistent and high-performance labeling solutions.
Plasma Surface Activation Treatment
One way to ensure quality with industrial marking systems outside of utilizing non-destructive UV laser marking is with plasma surface activation. Plasma surface activation treatment enhances the adhesion properties of surfaces, making sensitive and low-wettable wire materials more conductive to wire marking. This technique involves several steps:
- Preparation of the surface: Before treatment, the operator must clean the marking surface and remove any contaminants, such as oils, dust, or residual materials, that could affect the plasma activation process.
- Plasma generation: By exposing a gas to an electrical field, the ionization process begins and plasma is generated. This ionization creates a mixture of ions, electrons, and other reactive particles that can induce changes to the surface properties of materials.
- Exposure to plasma: The treatment then exposes this prepared surface to the energized plasma. This exposure takes place in a specialized chamber where a chosen plasma gas—such as oxygen or nitrogen, depending on the desired surface characteristics—replaces the ambient gas.
- Surface modification: As plasma reacts with the surface, it modifies its chemical and physical properties. The high-energy plasma particles bombard the surface, breaking chemical bonds and creating new functional groups that significantly enhance surface energy and wettability. This increase in surface energy facilitates better adhesion of inks or coatings applied afterward.
- Post-treatment handling: Once the treatment is complete, the surface is ready for marking or bonding. It is crucial to minimize handling or exposure to contaminants to ensure that the activated surface retains its improved properties.
This treatment improves the quality and durability of wire markings and ensures compliance with stringent industry standards.
Advantages of Plasma Treatment To Ensure Quality in Wire Marking
Plasma surface treatment is increasingly recognized as a superior method for ensuring quality assurance in industrial wire marking, chiefly due to its safety, efficiency, and environmental benefits. Plasma treatment is a non-toxic process that utilizes ionized gas to modify the material’s surface properties.
Plasma treatment offers enhanced control over surface modification, leading to consistent and high-quality adhesion of inks and coatings across various substrates, including difficult-to-mark materials. The process operates at a high speed, which enables rapid production rates without compromising on the clarity and durability of the markings. Plasma treatment stands out as an efficient, safe, and environmentally responsible choice for manufacturers committed to maintaining stringent quality standards in wire marking.
Challenges in Aerospace Wire Marking
One of the sectors where quality assurance in industrial marking is most important is aerospace. The aerospace sector presents unique challenges for industrial marking systems due to its demanding standards and diverse materials. Components in aerospace applications must withstand extreme conditions, such as high temperatures, intense vibrations, and exposure to various environmental factors.
These conditions necessitate precise, legible, and resilient markings to guarantee durability and traceability throughout the component’s lifecycle. The complexity of aerospace materials, including advanced composites and specialized alloys, can complicate the marking process. Achieving high-quality marks on these materials requires advanced technologies like UV laser marking.
UV Laser Marking for Aerospace Wires and Cables
UV laser marking has revolutionized the labeling of wires and cables in the aerospace industry. This advanced technology utilizes UV lasers to create permanent, high-quality marks by altering the color of the wire insulation without causing any damage.
The process relies on the absorption of laser radiation, resulting in a highly durable mark that withstands harsh conditions. The use of Titanium Dioxide pigment further enhances the durability and stability of UV laser markings, making them ideal for aerospace applications.
Tri-Star Technologies Wire Marking Systems for Aerospace Application
Tri-Star Technologies has established itself as a leader in the development of plasma treatment and laser marking systems, particularly in the aerospace sector, where precision and reliability are crucial. Their aircraft wire markings machines excel in challenging aerospace applications, seamlessly adhering to stringent industry standards such as Boeing BAC5152, D6-3691, MIL50881, and SAE ARP5607.
These machines utilize advanced UV laser technology, which ensures clean, high-contrast markings without damaging the substrate, making them ideal for marking components that require both durability and clarity. The precision of Tri-Star’s systems minimizes the risk of errors and enhances traceability, ultimately contributing to safe and efficient aerospace operations. By relying on Tri-Star Technologies, aerospace manufacturers can confidently meet regulatory requirements while ensuring the integrity of their products.
Partner With Tri-Star Technologies for Quality Industrial Marking
Guaranteeing quality in industrial marking is crucial for product integrity and compliance in industries like aerospace. Advanced technologies, such as UV laser marking and plasma treatment offered by Tri-Star Technologies, offer efficient, durable, and eco-friendly solutions. As these technologies evolve, manufacturers can expect further advancements in marking systems.
If you need an industrial wire marking system, Tri-Star Technologies is here to help. Learn more about our technology online or contact our staff to speak with one of our experts today.